The Covid pandemic has forced businesses to rapidly adopt new working methods. Manufacturing is no exception. In factories, thanks to highly automated CNC production machinery and careful social distancing, essential work has largely continued, but external face-to-face meetings with customers suddenly became highly restricted.
Manufacturing contractor ICEE Managed Services turned instead to remote meetings via Microsoft Teams, one of several popular business-oriented, video-conferencing platforms. As a result and coupled to using Solidworks, an advanced 3D computer-aided design (CAD) and modelling system, it was able to continue working closely with its customers, including Fuel Cell Systems Ltd (FCSL), a leading specialist in providing cutting-edge fuel cell applications.
Both companies gained significant benefits including higher productivity arising from no time-wasting travel, more opportunity to explore iterations, faster design reviews and for FCSL, reduced time to market. For ICEE, a company that already works across the United Kingdom, more online meetings mean even shorter order to delivery timescales, regardless of the customer’s location.

Post-Brexit, many would say companies like Fuel Cell Systems Ltd (FCSL) represent the kind of enterprise Britain needs more of, namely young, vigorous and innovative, specialising in applications of advanced and essential technologies, with major growth potential.
Fuel cells offer a proven, practical way to help counter global warming, achieve zero-carbon and provide an alternative, renewable source of energy. FCSL offers a range of products and services in that field, from consultancy to the supply of fuel cell devices, and complete solutions that include packaging fuel cells or refuelling systems into purpose-built enclosures for use in a variety of industries and applications.
Before HyQube, ICEE first became involved when FCSL required an adaptable enclosure for a power generation product to serve several different applications. It accommodates three hydrogen fuel cells linked together, producing a 12kW output.
Searching the web for a bespoke enclosure manufacturer resulted in a shortlist containing ICEE Managed Services. Based in Waterlooville, Hampshire, the company’s credentials were already enhanced by considerable experience in the application of hydrogen fuel cells and the production of their own product, a hybrid electricity generator for off-grid power supply.
Besides well proven design for manufacture expertise, ICEE uses advanced Solidworks 3D CAD modelling and offers modern, fully integrated CNC equipment for seamless production, all under one roof. What’s more, it makes prototypes, one-offs and batches of enclosures, including variants, providing all the resources sought by FCSL’s Chief Technical Officer, Tom Chicken.
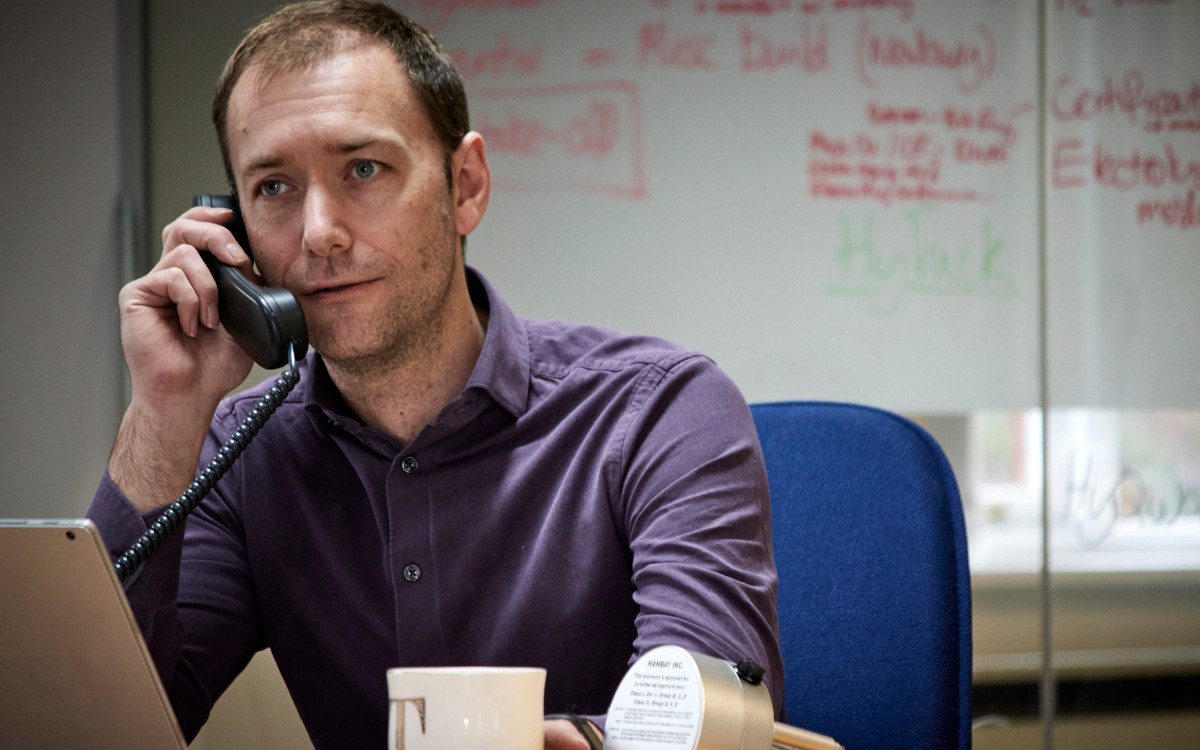
Goodbye face-to-face, hello video conferencing
FCSL began working with ICEE in October 2019. Tom Chicken sent the contractor concept sketches plus a specification, so these could be turned into a design for manufacture. The work was delayed until March 2020, but this coincided with the first Covid-19 lockdown, which prevented further face-to-face meetings.
Instead, in this instance, ICEE suggested using Microsoft Teams video-conferencing, a robust and popular collaborative system for remote working. Easy to use from anywhere with an internet connection, it enables work-in-progress meetings to take place without wasting time travelling and where necessary, supports working from home. Design details on Solidworks are displayed on-screen, modelled in three dimensions and manipulated dynamically in real time, as if all participants are sitting at their own CAD workstation.
“In some ways video-conferencing is better than face-to-face meetings,” says Tom Chicken. “I feel you still need the latter, but what Teams allowed us to do was quick reviews. ICEE would send out a 3D model beforehand, I could review it first and come up with questions.
“We would then have a three-way Teams chat, where we had the 3D model on the screen and I could talk through my alterations or modifications. Then they could say yes or no, or how easy it was to do, or make other suggestions. Most changes could be made immediately in real time. It meant we could all just get on with it, rather than having to arrange a time where we all had to drive somewhere to meet.”
Design of an enclosure is crucial
The first order was made for a fuel cell manufacturer, enabling FCSL’s customer to use the product as a test unit to evaluate an application. For another customer, a unit will provide electricity to run Europe’s first self-sufficient, highly publicised hydrogen-powered house.
Dimensionally, the enclosure looks like a nineteen-inch computer rack, but the similarity ends there. Inside, the hydrogen fuel cells located in the upper part of the enclosure generate heat. Cooling is achieved with thermostatically-controlled fans and ducting. ICEE has substantial experience in equipment enclosure design and in particular, the vital topic of cooling. This is because the company has a long history of designing and making batches of bespoke cabinets for customers in the telecommunications industry (and installing and maintaining those cabinets in the field). For example, units for the fast fibre broadband and related sectors contain kit that also generate significant heat. As a result, the contractor knows a lot about reliable temperature management and cooling, including ducting, ventilation, sensor and fan devices, to guard against over-heating and other risks.
With hydrogen and methanol fuel cells, providing the right protection and efficient cooling is key to safety. “The design of an enclosure is crucial, fundamental to the whole project,” says Tom Chicken. “ICEE’s experience in cabinet design, manufacturing and build is so useful. They already know about relevant details, such as how to design and fit a door and seals, how shelves can best be bolted together, or designing special ducting to go on the back of fuel cells to ensure hot air is only directed one way, safely.
“Whilst we are capable of designing individual parts and we’ve designed prototype enclosures in the past, ICEE’s existing and combined knowledge of design, manufacture, installation and maintenance is, I think, the key factor for us here.”
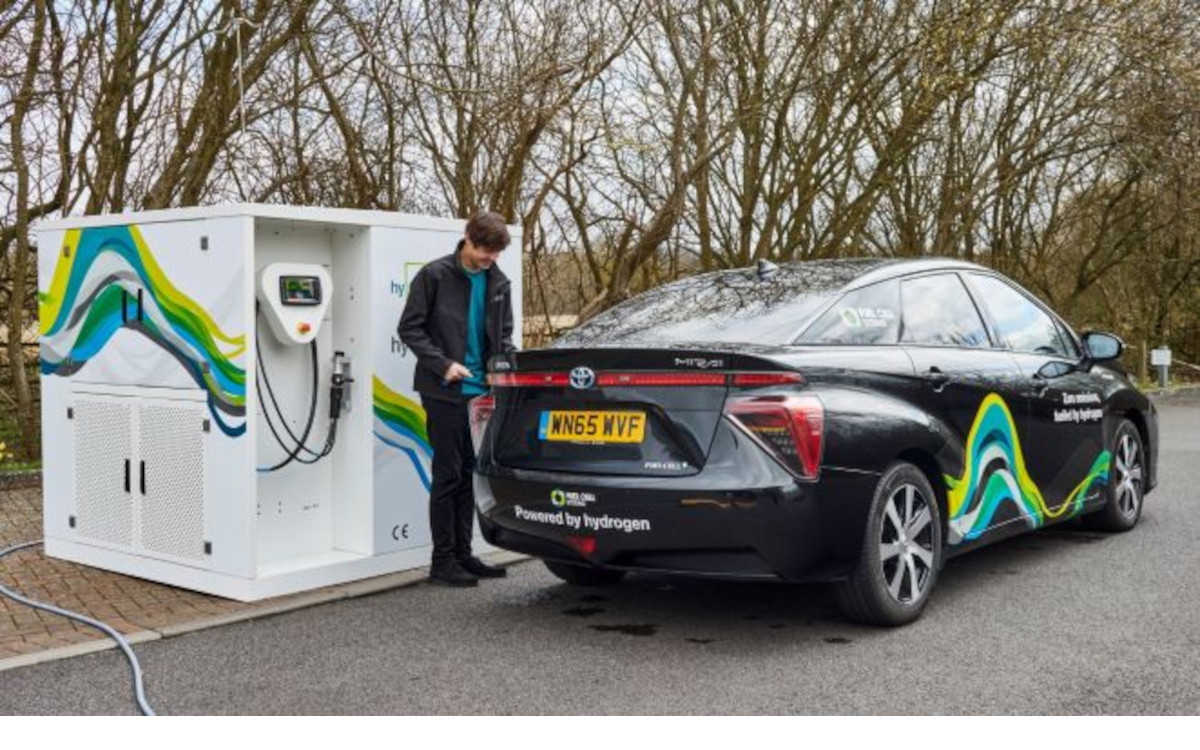
Virtual prototyping saves time, reduces risk
For some years and using the advanced features of its Solidworks CAD system, ICEE has done ‘soft’ prototyping on-screen. Often, a physical prototype is unnecessary, as the design for manufacture software is so well developed it is possible to go straight from the screen into production.
There are several major benefits. All possible issues and risks may be identified and rectified at this flexible stage. More iterations may be usefully explored in less time. Thanks to optimisation capabilities, sheet metal components may be pre-checked for the best and least costly way to cut or profile a part. It all ensures functionality and fabrication is right-first-time, rather than finding out costly mistakes after one or more physical prototypes are made. Waste is minimised or eliminated, reflecting true lean manufacturing principles.
“That’s the way everything is going now,” says Tom Chicken, “3D modelling packages are so accurate you don’t need to build something first.” But he adds, “. . . sometimes you just need to see the physical structure before you can fully understand the possibilities.”
A case in point is the FCSL HyQube mobile hydrogen refuelling product the fuel cell specialist designed and developed, part of a range of refuelling options offered for different transport sectors. This is a 1.8m square structure, housing hydrogen tanks and electrical plus fuel delivery systems, used outside in the open air.
Before ICEE became involved, a prototype enclosure had been built by a local fabricator from steel sheet metal. Evaluating this ICEE suggested a number of changes, aimed at making the product less costly to make, but maintaining the high quality FCSL demanded. For example, using aluminium parts and panels to reduce weight and improve weather resistance; bolting parts together rather than welding to reduce costs.
FCSL expect a healthy demand for this product, so getting design for manufacture right and hence economic to produce is very important. Again, MS Teams and Solidworks were used by ICEE, but in this case from start to finish. Video-conferencing has been around a long time now, but thanks to the latest internet technologies and today’s wide choice of platforms it looks set to continue beyond lockdowns and become far more commonplace.